今日は、先日行ってきた第21回インターフェックスジャパンのセミナーについての備忘録です^^
馴染みのない方が多いと思いますが、インターフェックスジャパンは医薬品や化粧品、洗剤の製造・包装展。
メーカーさんが製造装置を選定したり、新しい技術を取り入れたりするための展示会です。
私も去年の今頃はプラントを設計していたため…
攪拌装置やら測量計、運搬装置、粉砕装置、クリーンルーム、集塵機、清掃機、洗浄機、忌避剤まで…
あれやこれや気になって、一日じゃ全然時間が足りなかったのですが、今年はさすがにあまり見るものがなかったですね(^^;)
商談しないのにじっくり見るのも申し訳ないので珍しい乳化装置だけちょちょっと見て、あとは遠めに見て返って着ちゃいました(゜-゜)
AI, IoT関連の展示はまだまだ少ないかなぁ?という印象です。
AI / IoT展があるからここでは出展しないのでしょうか。
この日の目玉は特別講演【大手化粧品・洗剤メーカーが挑む工場改革の最前線】で、
演題は『資生堂における協働型ロボットの導入と展開』
(株)資生堂 生産部 生産基盤強化グループ那須工場 製造部準備グループ グループマネージャー 小林穀久氏
『グローバルマザー工場としての人財育成、成長への取組み』
花王(株) 和歌山工場長 松下芳氏
の二題でした。
特に、資生堂の講演時は立ち見が出る程!
いつもの記事とは毛色が違う“ものづくり”についてですが、とても面白かったので、共有させて頂きますね^^
ところで、資生堂は毎年工場増設中なのだそうです。インバウンド景気が好調とはいえ、すごいですよね…!
今年の冬に那須工場を新設し、来年は大阪工場、再来年は福岡の久留米工場と怒涛の新設ラッシュです!
数年前までは、安価な人件費を求めて製造業を中心に生産拠点を海外に置くメーカーが多かったですが、新興国の人件費高騰や海外の転職志向による技術伝承問題がありました。
工場を徹底的にオートメーション化をしてしまえば人件費問題も小さくなるため、自働化を腹に決めたメーカーは輸送費のかからない国内へ生産拠点を移してきているように思います。
特に、化粧品は「MADE IN JAPAN」が大きな価値にもなります。
久留米の工場はIoT技術も積極的に取り入れるということで、フルオートメーションラインも取り入れるのではないでしょうか^^
今日伺ってきたお話はそのような大規模な夢工場構想!のお話ではなく、資生堂が取り入れつつある協働型ロボットの導入事例についてでした。
ロボットと聞くと、皆さんはどのようなイメージを思い浮かべますか…?
こんな感じ?笑
AIBOやペッパー君も立派なロボットです^^
ちなみに、私にとってロボットとは
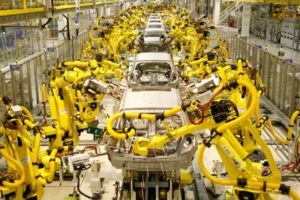
https://roboteer-tokyo.com/archives/10230より引用
産業用ロボットです笑
ロボット化は自動車業界の方が進んでいますね!
理由は部品が重くてロボット使わないとやってらんない!ということもあると思います(^^;)
安全面や品質面、生産性においてロボットの活用はかなりメリットがあります。
そのために部品の規格を共通化したりするんですね(^^)
一方、化粧品は手に取った時の感動があってなんぼの商品ですので、
容器の形状は多種多様ですし、シーズン毎に新商品がリリースされたりと、品種の切り替えが目まぐるしい業界です。
また、自働化の難しさの一つに”検査”があります。
人間の目は、カメラでは識別できない絶妙な色味の違いやキズに気付くことができます。
(外観検査のデメリットとして、熟練すると検査がどんどん厳しくなったりします(^^;笑)
小林氏が言うには、「化粧品の検査は【人の感性】に勝るものがない」ということでした。
資生堂は化粧品をまるで芸術作品を作るかのように扱っているのだそうです。フルオートメーション化の難しさが伺えます。
とはいえ、来たる省人化時代。
国内の人口減少は避けられないですし、情報社会におけるコスメトレンドは非常に移り変わりが早いです。
思考の多様化によって「自分だけの色を数種持ちたい」という女性のニーズから小ロット生産が増加していることも事実ですが(資生堂は売れている商品の半分が小ロットだそう!)、
毎度の専用機開発はかなり大きなリスクですが、多様な形状に対応する自動化ラインは難易度の高い課題と言えるでしょう。
そこで打ち出した試作は、「自分たちの設備は自分たちで」。
社内のメカニックエンジニアを育成し、品種の切り替えが容易なラインを自分達で数台作製したのだそうです!
「餅は餅屋」とはよく言いますが、餅屋さんに任せず自分たちで餅を作るという…
流石、天下の資生堂です!
とはいえ、さすがにロボットを製作する訳にはいかないので、様々なメーカーのロボットでトライしたそうです。
その中で選ばれたのがカワダロボティクス(株)製の「NEXTAGE (ネクステージ)」。
2013年度のグッドデザイン賞も受賞しているんですね。
繰り返し工程や重労働作業、複雑工程・繊細工程などの人の作業に価値を生まない工程はロボットの作業とし、
判断のいる作業、人の五感に頼る検査と作業、管理作業などを人の役割としてロボットの導入を考えていったそうです。
例えば口紅の製造工程では、色味や細かい傷などの外観検査は人が行うべき作業です作業です。
一方、蓋がけ作業は単純な繰り返し工程ですが、柔らかい口紅は少しでもぶつかると不良となってしまい、一日中行うには繊細で負担の大きい作業です。これをロボットに置き換えることで、作業者の負担や不良率の低減が可能になります。
ところで、ロボットを導入する際、開発に苦労するのはロボットハンドと呼ばれる手の役割をする部分です。
掴む・挟む・吸引するなどの目的に応じた動きと大きさが必要なのですが、意外とちゃんと持ってくれなかったり、近くの設備に干渉してしまったりするんですよね(^^;)
また、ロボットの動きをプログラムする前は人が操作するのですが、意外と衝突しまくります!しかもゆっくり動かしているつもりでも、衝突時はメリメリと周りを破壊したりします(^^;)←元製造業エンジニア
そのようなエラーは不慣れだと特によく起こるものですが、すぐにハンドを直してリトライするために、3Dプリンタで作成したのだそうです!
金属の3Dプリンタは、設備も材料もとってもお金がかかるものですが、確かに予期せぬ衝突の度に外注していたら、開発期間が読めなくなってしまいますもんね。
この口紅の製造工程ではロボット導入の結果、1ライン辺り2名の省人化を達成したそうです!
張単純計算で恐縮ですが、1日1万円/人、20日間/月,200日/年稼働の計算で、8000万円の削減!
不良率も低減したら、投資金額も数年で回収できちゃいそうです。
また、ロボット故障時にも生産が止まらないように、ロボットを引きずり出して人が作業できるようにするなどの工夫も。
化粧品のような小さな商品を扱う小さなロボットの利点が生かされていますね!
パウダーファンデーションのリフィル製造工程では、箱の組み立て・箱詰め検査・重量検査などの工程を全てロボットが実施し、しかもハンドを変えずに複雑工程をこなすのだそうです!
すごいですー。グローリーとの共同開発だそうですが、優秀なエンジニアさんなんだろうなぁ…
ロボット技術は確実に進化しており、これまで出来ないと思っていたことを次々と達成しています。
しかし、ロボットは万能ではありません。ロボットに何をさせて何をさせないのか?明確に区別することが重要です。
小林氏が言うには、ロボットによる自動化でキーになるのは、部材の供給と工程設計。製品終了後、同じロボットで別工程の自動化に取り組める生産技術力が多品種生産でのロボット活用の重要要素とのこと。
化粧品で課題とされていた多品種生産での自動化の解決策は、汎用性のあるロボットの開発と言えそうです。
生産ラインの自動化は、不良率を低減し製品コストを下げることができます。
またトレーサビリティーが容易になり、品質向上にも大きく貢献するでしょう。
もちろん簡単に達成できることではありませんが、品質の良い化粧品が安価に手元に届けば、私たちにとっても嬉しいことです^^
人手不足のピンチを技術力向上のチャンスと捉えて、各メーカーさんには頑張って頂きたいですね!